- Solar energy blog
- Rare metals in the photovoltaic industry
Rare metals in the photovoltaic industry

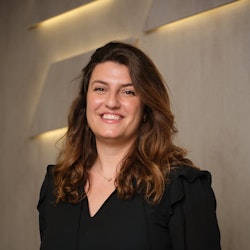
Laura Rodríguez
Business developer
Laura is a renewable and software industry sales professional, currently working at RatedPower as Sales Overlay in North America & Territory Manager Oceania. With a background in International Business and International Trade, Laura previously worked in the business strategy area in various companies as well as as a market analyst for the Government of Spain in Australia.
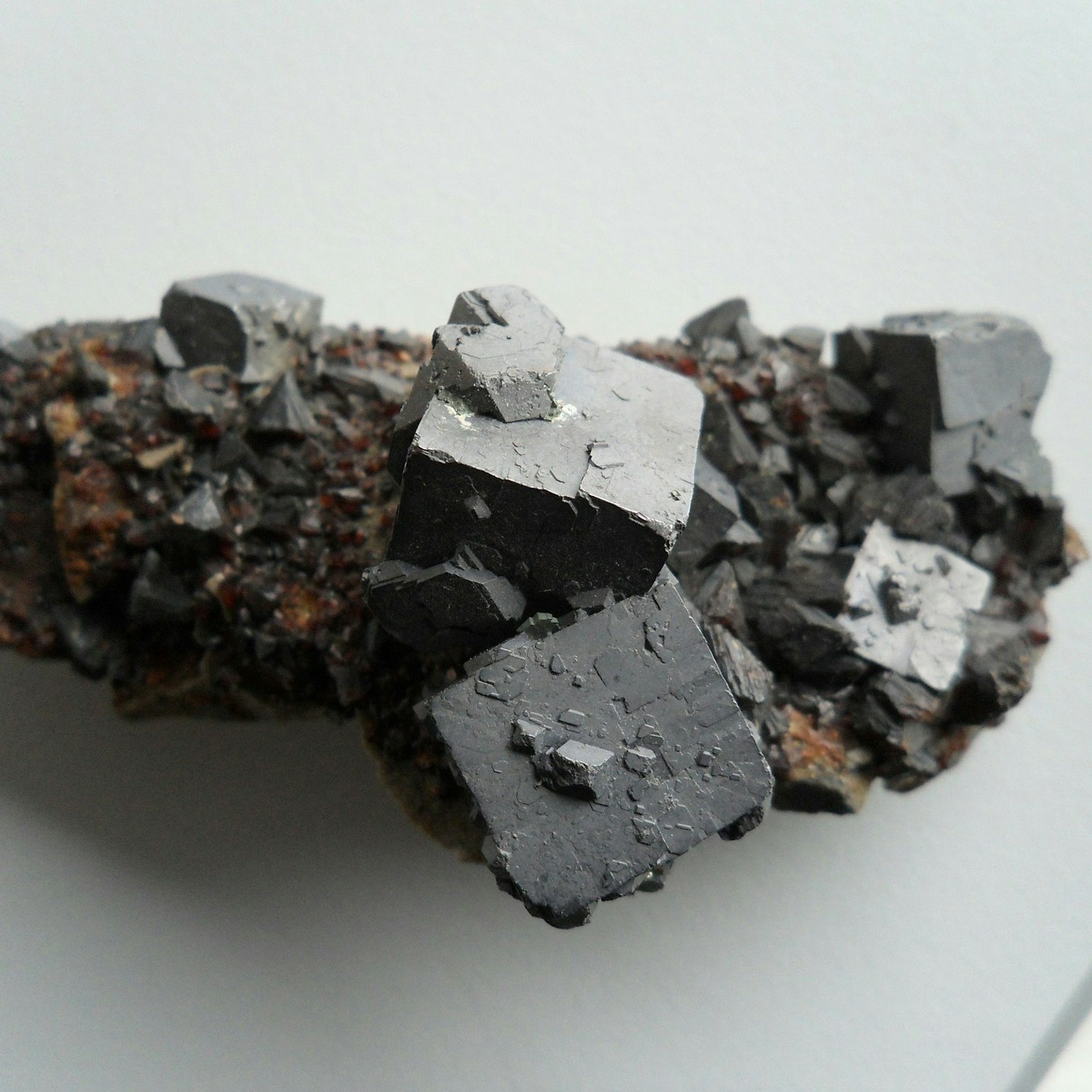
Content
Rare earth elements (REEs) play a key role in the green energy transition. They are used extensively in wind turbines and electric vehicle powertrains. But there are concerns about the dependence of the global supply chain on China, especially in light of its trade war with the US in recent years.
What are rare earth elements? How are they used in the renewable energy industry and what alternatives does the solar photovoltaic (PV) sector offer? Let’s find out.
What are REEs and how are they used in clean energy?
Rare earth materials are so called not because they are rare in the earth’s crust, but because they are chemically very similar. This makes them difficult to mine and separate without a costly and polluting refining process.

There are 17 REEs in the periodic table, comprising the lanthanide series, yttrium, and scandium. Neodymium, praseodymium, dysprosium and to some extent terbium, are used in the permanent magnets that turn wind turbine generators. Rising prices have increased the substitution of dysprosium and terbium in neodymium iron boron (NdFeB) magnets to keep down costs as prices have risen in recent years.
A 3MW direct drive turbine contains close to 2 tons of rare earth permanent magnets. Neodymium, dysprosium, and praseodymium magnets are also used in electric vehicle (EV) motors, each EV containing around 1-2kg of magnets. Demand for rare earths is expected to rise sharply in the coming years in response to the growth in wind turbine installations and electric vehicle adoption.
Based on the sustainable development scenario from the International Energy Agency (IEA), demand for neodymium alone in low-carbon power generation and EVs could climb by more than 600% from 4,900 tons in 2020 to 37,700 tons in 2040. Its share in clean energy technologies would rise from 16% to 41% over that period.
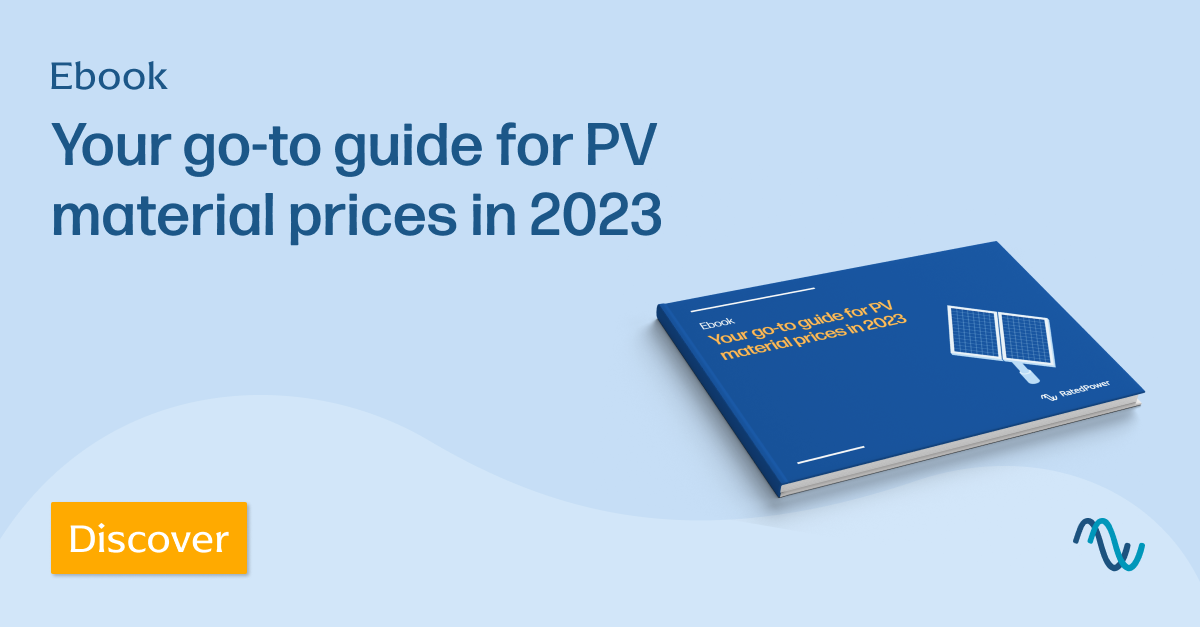
Explore the outlook for PV material prices in 2023 and how market factors have affected costs with this free eBook.
China accounts for the lion’s share of the global REE market, from mining, through to separation and refining
Around 85% of global rare earth production capacity is in China. Australia and the US are among the countries developing new facilities to reduce reliance on Chinese supply, particularly as REEs are also used in military equipment and tightening supply has prompted China to increase export restrictions.
REE prices climbed earlier this year to their highest levels in close to a decade as rising demand in China and COVID-19 restrictions have tightened the market.
Minor metals in the solar industry
Unlike the wind power and EV sectors, the solar PV industry isn’t reliant on rare earth materials. Instead, solar cells use a range of minor metals including silicon, indium, gallium, selenium, cadmium, and tellurium. Minor metals, which are sometimes referred to as rare metals, are by-products from the refining of base metals such as copper, nickel, and zinc. As such, they are produced in smaller quantities.
While minor metals like gallium and tellurium are largely produced in China, silicon has more diverse sources of supply -- including Russia, Norway, and Brazil. Indium and cadmium are refined in South Korea, Japan and the Americas as well as China, while selenium is produced in Europe and Japan in addition to China.

Solar panels and silicon
PV cells contain semiconductor materials that absorb light and transfer it to electrons that form an electric current. Silicon is still the dominant semiconductor metal used in solar cells, accounting for more than 90% of the market. Thin-film technologies account for the remaining share, in the form of copper indium gallium di-selenide (CIGS) and cadmium telluride (CdTe).
Solar panels using crystalline silicon-based semiconductors are the most efficient, with a maximum achieved rate of 26.7%, while CIGS cells have an efficiency record of 21.4% and CdTe has a record of 22.1%, although efficiencies are slightly lower outside of lab conditions.
As the adoption of solar energy grows, demand for silicon for PV panels could rise to 807,500 tons by 2040, up from 390,00 tons in 2020, according to the IEA’s projections. If thin-film technologies gain more market share from silicon, demand for cadmium and tellurium could rise as much as sevenfold, while demand for gallium could reach 10 times more than current production.
Prices for polysilicon, the form of silicon metal used in PV panels, have climbed over the past year as demand has outpaced supply and disruption to production at facilities in China has further tightened the market. Other minor metal prices have also risen on supply constraints during the COVID-19 pandemic.
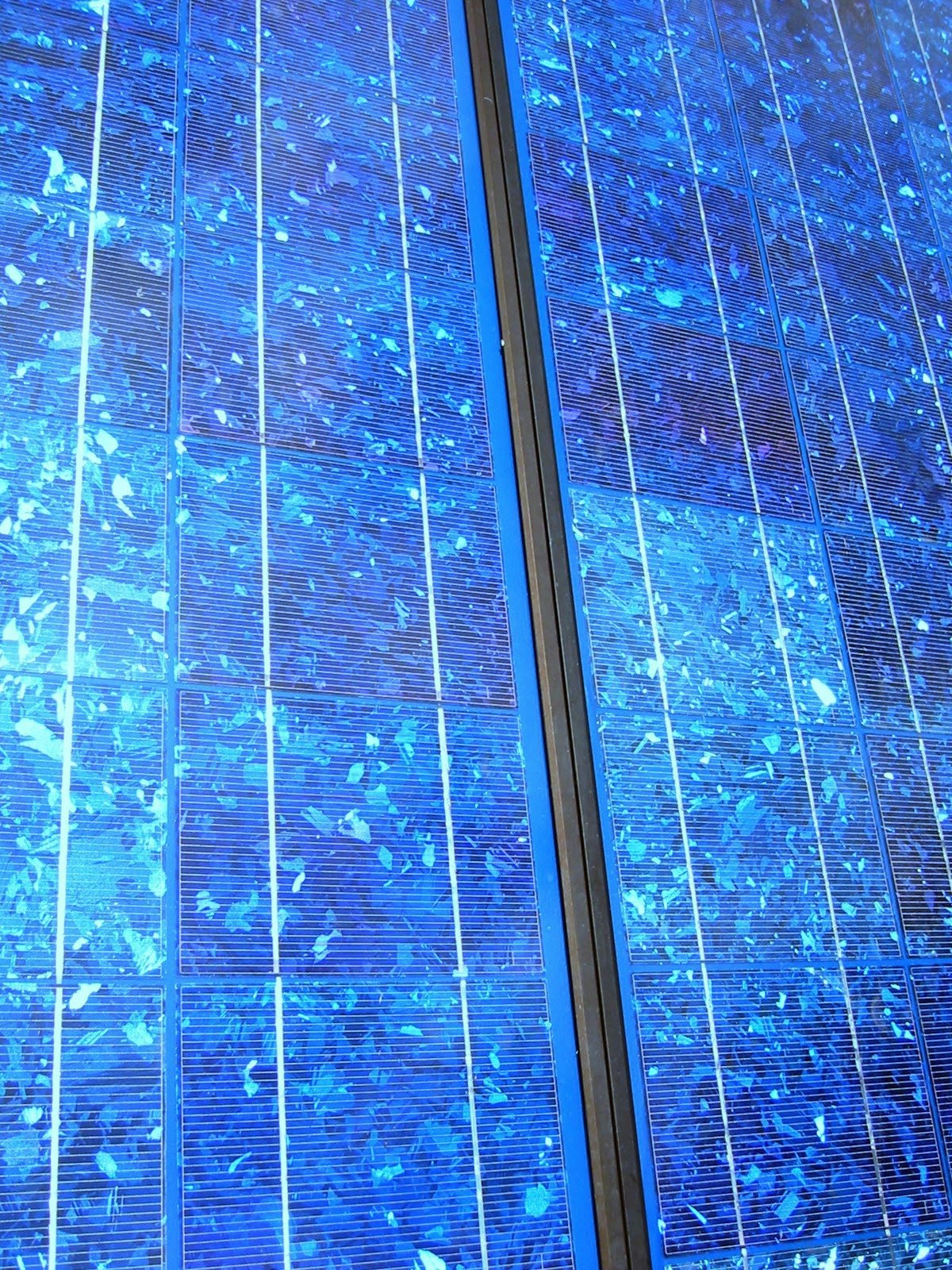
Alternative PV materials
Solar technology developers are exploring the use of new materials for PV cells as the industry looks to increase cell efficiencies, reduce costs and differentiate in a crowded market.
Perovskites
One of the most promising developments is perovskite cells. Perovskites are compounds of calcium-titanium oxide or other materials that have the same crystalline structure. Companies such as Oxford PV in the UK are producing solar cells that layer perovskite crystals with silicon to produce more efficient panels at a lower cost.
Oxford PV has reached a record efficiency of 29.52% for its technology. Polish company Saule opened its commercial production facility in May and announced its first installation on a factory façade in August.
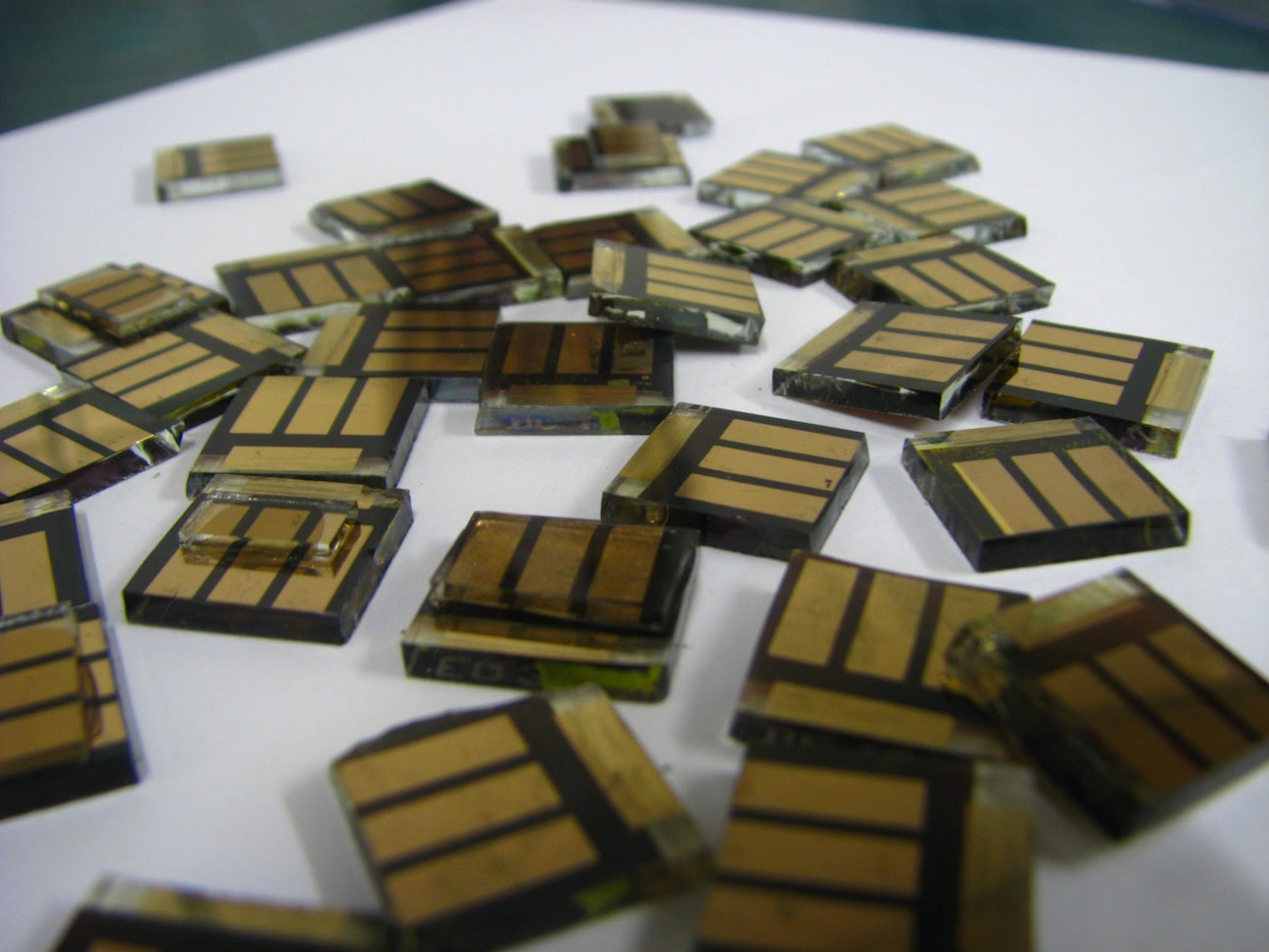
Perovskite tin solar cell, via University of Oxford Press Office.
Organic PV
Using organic compounds allows developers to create transparent or colored PV cells that can be applied to various materials including flexible plastic. Although developers are facing challenges in achieving efficiencies above around 11% while maintaining stability, the technology is showing promise for building-integrated PV materials and wearable fabrics, because it’s cost-effective, lightweight, and flexible.
Dye-sensitized cells
Dye-sensitized solar cells (DSSCs) are indium tin oxide (ITO) or fluorine-doped tin oxide thin-film cells. The cells are coated with a thin layer of titanium dioxide and a dye solution, made from ruthenium or organic compounds, bonds to the titanium dioxide. DSSCs perform well in low light conditions, including indoors, can be made in different colors, and offer low production costs. In May, Sweden-based Exager raised $38 million to build a second factory for its solar cell material for wearable products such as headphones, helmets, and workplace protective gear.
Quantum dots
Quantum dots are nanoscale particles that offer a straightforward way to process and deposit semiconductor materials onto substrates for solar cells. There are various sizes and they have a customizable bandgap that enables them to capture more light. But difficulties in creating electrical connections between quantum dots have so far kept maximum efficiencies around 11%.
CTA: Download our Renewable Energy and Solar Research Report to read about the trends that will drive the renewable industry forward.
2025 Trends: Renewable Energy & Solar Research Report
Get key insights and data from an industry-wide survey and solar simulations on the RatedPower platform. Download now to uncover critical trends and challenges shaping the future of renewables.
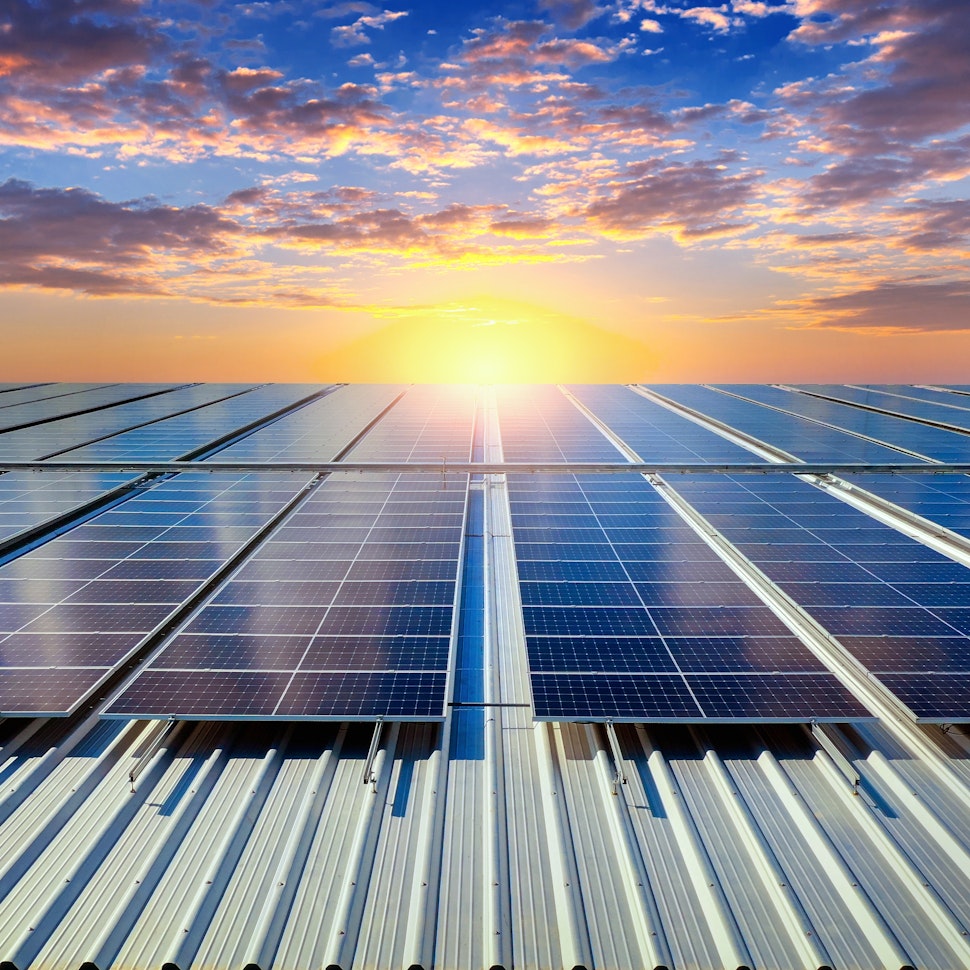
Latest stories
Related posts
Technology and engineering
The green hydrogen boom in LatAm
Latin America is emerging as a green hydrogen leader. Learn how LatAm countries are leveraging solar and wind power to drive green hydrogen production.
Updated 22 JUL, 25
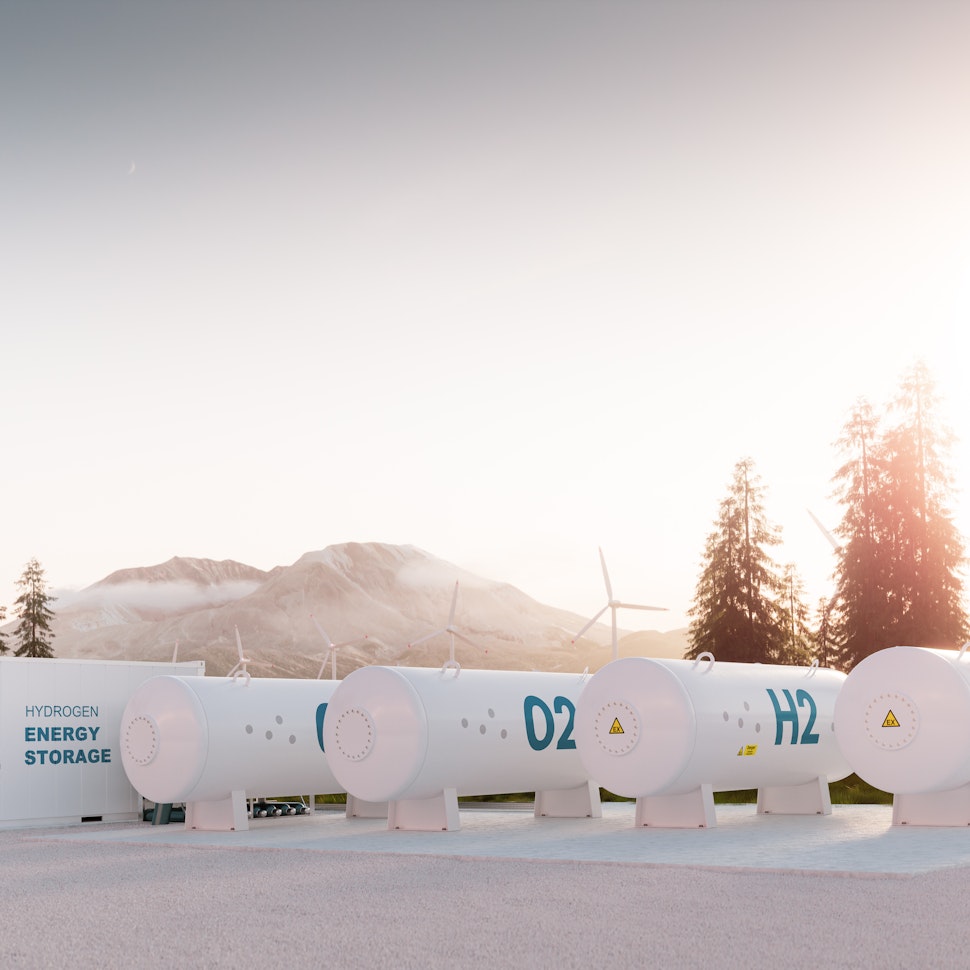
Technology and engineering
Innovation in renewable energy: Developments expected in 2025
We look at the 10 biggest renewable industry developments that are making a green future possible, including perovskite solar cells, green hydrogen, and more.
Updated 18 MAR, 25
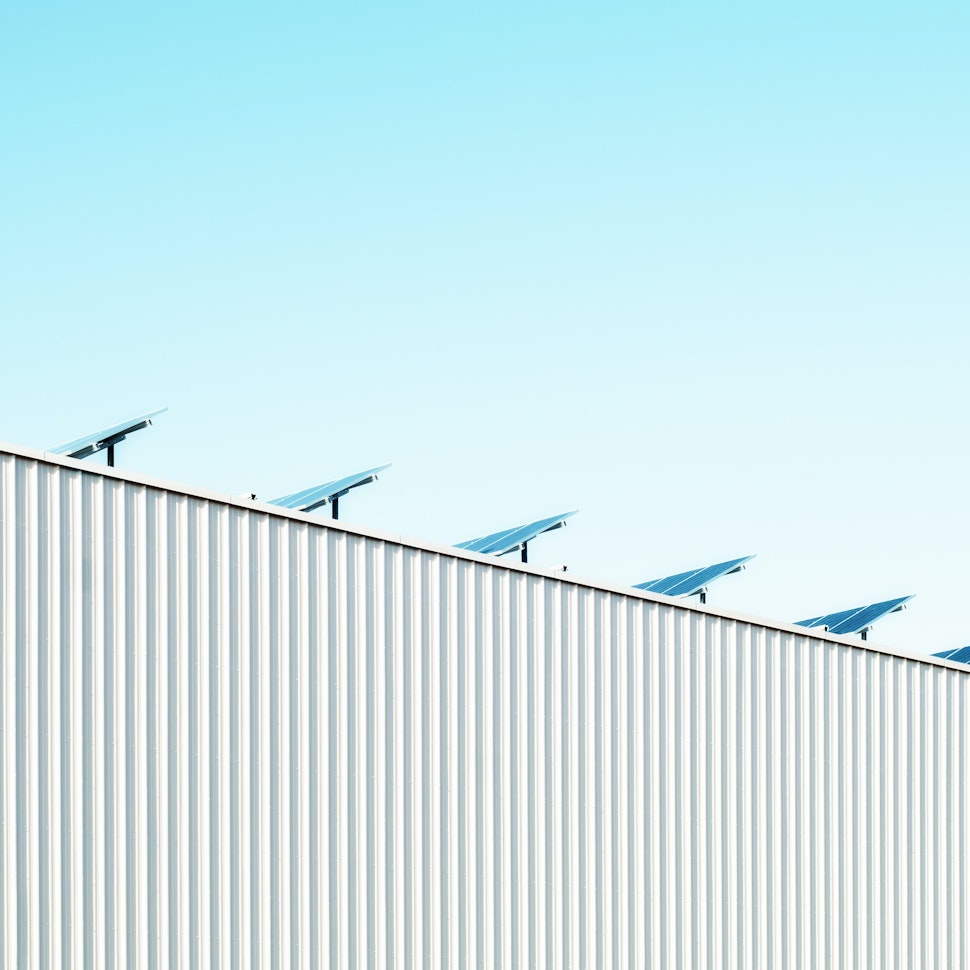
Technology and engineering
What the future holds for the longevity and efficiency of solar panels
Tests done by the French photovoltaics group Hespul showed that the panels, installed in 1992, are still operating at an astonishing 79.5% efficiency. Read on to find out more.
Updated 4 MAR, 25
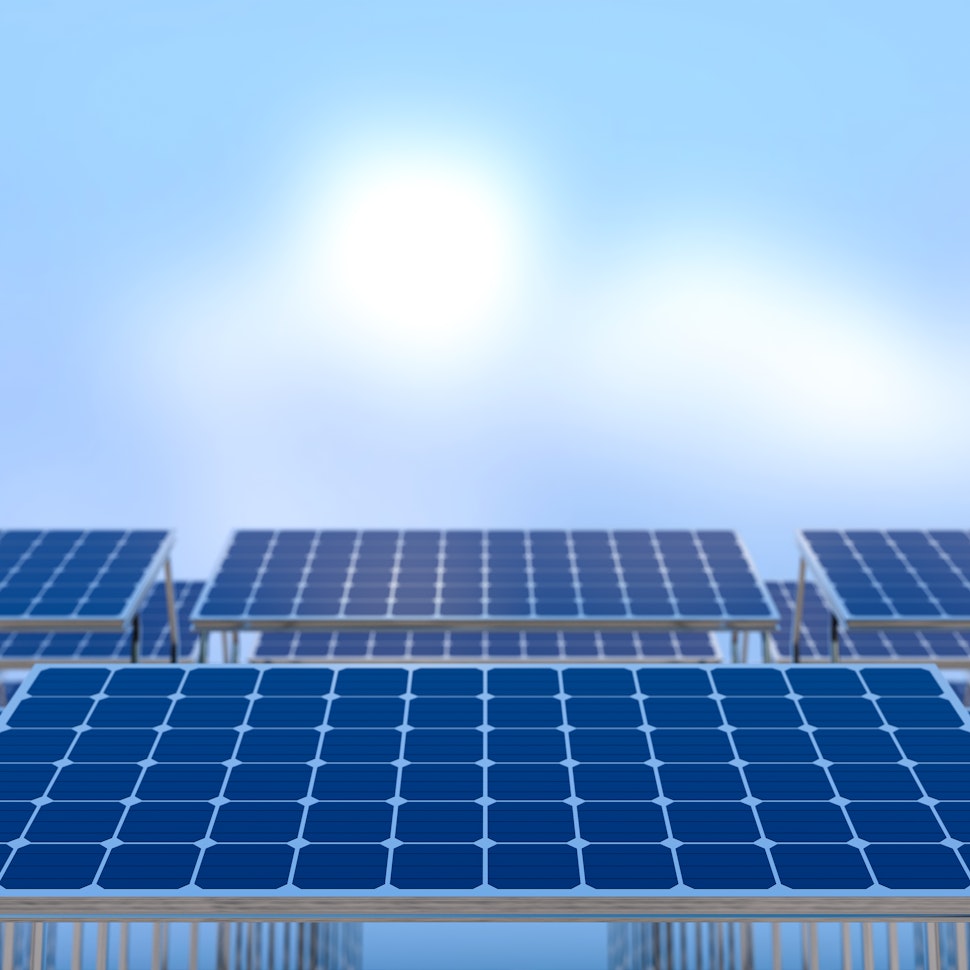
- RatedPower
- Solar energy blog
- Rare metals in the photovoltaic industry